Vision - we need to broaden the discussion on the circular economy
30 October 2023 Gerd Müller
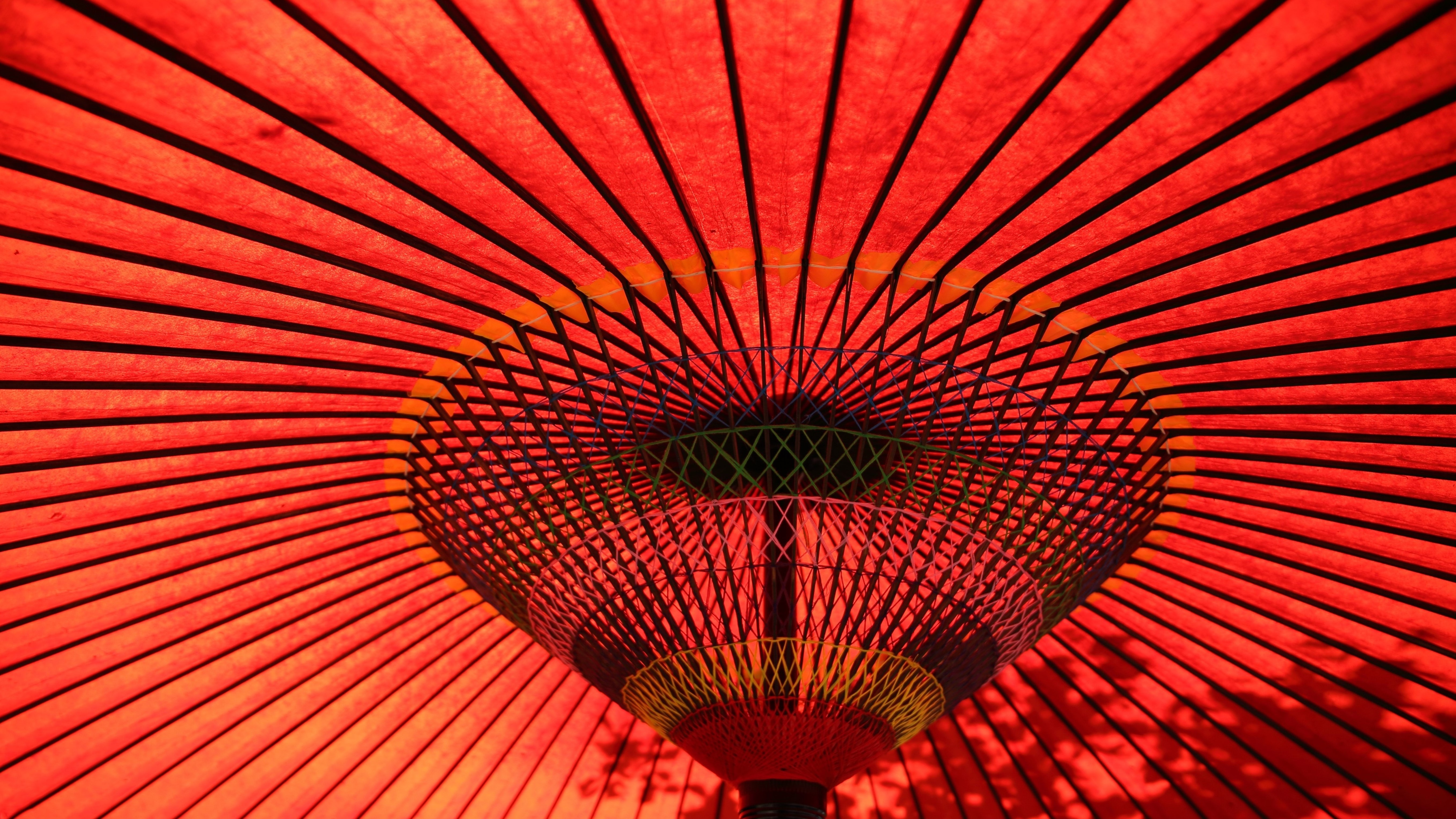
Our current linear “take, make, dispose” economic system depends on a permanent throughput of materials. These are extracted, traded and processed into goods, which are then sold and used, and finally disposed of as waste or released as emissions.
Over the last century, the global economy has witnessed a surge in material extraction and use.
Between 1970 and 2017, the annual global extraction of materials tripled, growing from 27 billion tonnes to 92 billion tonnes. Today it is over 100 billion tonnes - a figure driven by both the high levels of material consumption in rich countries and the rapidly growing needs of emerging economies.
Just think, on our planet Earth there are now more than one billion motor vehicles, two billion personal computers, and more mobile phones than there are people – more than 7.6 billion.
Earth Overshoot Day marks the date when we have used all the biological resources that the Earth can renew during the entire year. Each year, Earth Overshoot Day is earlier and earlier. This year it is 2 August.
If we carry on as we are, by 2050, global demand for virgin materials is expected to at least double again!
But it is not just a matter of the world eating into a finite supply of resources. The current pattern of resource use is having negative impacts on the environment and on human health. Resource extraction and the processing of these resources into biomass, fossil fuels, metals and non-metallic minerals make a massive contribution to the global greenhouse emissions that are over-heating our climate. It is also driving global biodiversity loss and water scarcity: the extraction and processing of materials is responsible for around 50% of carbon emissions and 90% of global land-related biodiversity loss.
Materials extraction and production and the distribution and use of products also contribute massively to environmental pollution and especially to air pollution. Air, water and soil pollution is the largest environmental cause of disease and death in the world today, responsible for an estimated nine million premature deaths in the year 2019.
Another insurmountable challenge for the linear economy is how to dispose of the ever-increasing amounts of used, broken or otherwise unwanted products. Municipal solid waste has reached levels that means traditional waste management approaches are struggling to cope.
There is just too much waste. Landfills are overflowing. Waste incineration is creating and/or releasing harmful chemicals and pollutants. Our rivers and oceans are filling up with plastic. Looming resource scarcity, environmental pollution and an overwhelming amount of waste show that the current system is no longer working for businesses, for people or for the environment. The take-make-use-dispose economic system cannot go on.
To create a thriving economy that can benefit everyone within the limits of our planet, we need to transform the way we manage resources, the way we make and use products, and the way we deal with products when they break or wear out.
We need a circular economy which uses renewable energy, ends the use of toxic chemicals, and aims to eliminate waste by way of superior design of materials, products and systems.
Moving towards a circular economy creates substantial benefits in terms of resource availability, profitability, new economic activity and, last but not at all least, an improved environment.
One of the basic principles on which the circular economy is based is a focus on design. For any product, decisions made at the design stage will influence what will happen to that product – how it is made, used and disposed of, and whether it will end up in an incinerator or a landfill or in the sea. The essential ideas here are to view waste and pollution as design flaws, to rethink product design and production processes, and to harness existing and new materials and new technology to ensure that waste and pollution are not created in the first place.
Design choices also come into play in determining whether a product can be repaired, recovered, remanufactured or composted. Such design choices include: the type of materials a product is made of; the application of a modular design approach; the way a product is assembled and the ease of disassembly, so that it can be maintained or so that its parts can be replaced and/or reused; and the capacity for a product to be upgraded or improved in the future.
As we say at UNIDO: progress by innovation!
In terms of industrial production, if products are designed so that they can be reused, repaired or remanufactured, the amount of resources needed would be greatly reduced. While reuse and repair extend the life a product, inevitably there will be a certain deterioration in effectiveness or performance. Remanufacturing, on the other hand, is a process in which a product or component that has worn out, or for some other reason is no longer functional, is restored to same-as-new or better condition and performance. The process takes place in line with specific technical specifications, including engineering, quality and testing standards, and typically yields fully warranted products.
Remanufacturing is an industrial process involving the dismantling of a product that has already been used, restoring and replacing components, and then testing the individual parts and the whole product to ensure that it is within its original design specifications.
In the United States remanufacturing emerged during the Second World War, focusing on military equipment. Later, in the second half of the twentieth century, it was taken up in Europe too, with the focus shifting to automobiles.
Today, it is typically applied to high-value equipment or components, such as engines and motors, transmission assemblies and gearboxes, complex medical equipment and tools, and heavy transport equipment, but also to office furniture, vehicle tyres, and printing and food-service equipment.
Developing countries are increasingly active in remanufacturing, especially in Asia, where China is a leader, having started to promote remanufacturing in 2006. Today, UNIDO is working with the Chinese authorities on a project to promote eco-design concepts in the field of industrial design.
In India, where remanufacturing is largely limited to a few sectors like heavy-duty vehicles and printer cartridges, UNIDO works with the Re:CREATe India Research Foundation to catalyze and advance the country’s remanufacturing potential.
In Indonesia and Malaysia the sector is growing, while Singapore set up the Advanced Remanufacturing and Technology Centre in 2012 to facilitate collaboration among companies and researchers in the field of remanufacturing as well as repair and restoration technologies, adaptive robotic welding and laser metal repair technologies.
In Latin America, the Japanese multinational, Isuzu, and the US company, Caterpillar, are leaders in the remanufacture of vehicle engines. In 2017, the Japanese company, Komatsu, opened a huge plant for the remanufacturing of electrical and mechanical equipment in Santiago, Chile. Also in Chile, UNIDO works with the CEO of Neptuno Pumps, which remanufactures water pumps for the mining industry. Petar Ostojic, who has been recognized as the “first promotor of circular economy in Latin America” by the World Economic Forum, helps UNIDO to advocate for remanufacturing as a new industrial approach to preserve nature and reduce greenhouse gas emissions.
New digital technologies now offer a way to expand the scale of remanufacturing by allowing remanufacturers to know much more about the way products are used, their location and the actual functioning of the product in terms of wear and tear. This information will enable them to maintain and upgrade products more easily.
Extending beyond the product itself, design decisions relating to the business model play a crucial role. The essential idea here is to shift from simply selling a product to providing a service. Customers access what they need, rather than owning things outright. The service provider or manufacturer will take care of maintenance and repairs because it’s in their interest to keep that item in circulation.
An example of this circular business model in the industrial sphere is chemical leasing, which has been pioneered by UNIDO since 2005. Chemical leasing is a product-as-service business model that shifts the focus from increasing the sales volume of chemicals towards a value-added approach. A producer sells the functions performed by the chemical, and functional units are the main basis for payment. The conventional approach is turned upside-down: economic success no longer depends on the volume of chemicals sold, but on the service that is linked with the chemicals.
UNIDO places great importance on applying innovative concepts to the real world. We are working to introduce circular practices into production processes. We are guided by the conviction that systems can be regenerative and underpinned by design principles that view final disposal as the very last option.
We are aware though that the circular economy is not just about a few manufacturers changing some of their products. It requires all the interconnecting companies that form our infrastructure and economy to come together to rethink the way they collectively operate.
While the circular economy is gaining ever greater traction in the industrialized countries, for UNIDO the message is that it offers a promising alternative strategy for industrial development and job creation in developing countries. It provides new opportunities for economic diversification, value creation and skills development.
Developing countries are in a good position to take advantage of these new economic opportunities. The strong tendency to value products and their components leads to a wider application of circular economy principles. Having products repaired and reusing them are more socially acceptable. With sufficient priority accorded to related investments, developing countries could ‘leapfrog’ in digital and materials innovation, and embed circular economy principles at the heart of their economies.
Success now in embedding circular principles in industrial development strategies can address the needs of growing, urban populations. It will also mitigate against a continued rise in primary resource use, and associated greenhouse gas emissions and environmental pollution.
We need to widen the global circular economy conversation to greatly increase the involvement of developing countries. We need to invest political and financial capital in promoting the development of inclusive circular economy approaches globally.
Developed country governments have an important role to play in piloting approaches and facilitating a dialogue on how the international dynamics of circular economy policies can be managed better. Support from international agencies, in particular UNIDO, will be critical to help small and medium-sized enterprises in developing countries and to demonstrate the viability of cross-border circular value chains at scale.